Don’t let the term “prefab home” scare you away — today’s prefabricated homes (also termed “building systems” by the National Association of Home Builders), are downright fabulous.
Not only do they provide home buyers with a custom, energy-efficient building solution, they’re also typically more affordable than traditional stick-built homes. While the total cost of a prefab home is highly variable based on size, amenities, and location, you can expect to pay between $100 and $220 per square foot, which often includes the home’s interior fixtures and amenities.
What Are Prefab Homes?
Essentially, prefab homes are homes that are constructed in a factory before being shipped to a building site in pieces, where they’re then assembled on-site in a matter of days. Unlike manufactured or mobile homes, which must meet the federal building code administered by the U.S. Department of Housing and Urban Development (HUD), prefab homes must be constructed according to state or local building codes.
This makes them a widely-accepted form of new construction, not subject to the same zoning restrictions that frequently limit the placement of manufactured and mobile homes. In other words, prefab homes must meet the same building codes as traditional “sticks and bricks” construction, so you can build a prefab home practically anywhere.
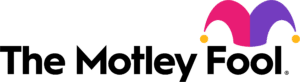
Motley Fool Stock Advisor recommendations have an average return of 372%. For $79 (or just $1.52 per week), join more than 1 million members and don’t miss their upcoming stock picks. 30 day money-back guarantee. Sign Up Now
Also, like traditionally-built homes, prefab homes typically qualify for construction and home loans, so you don’t have to have the total home cost on-hand. And in some cases, prefab home manufacturers are prepared to help you find appropriate financing (sometimes offering in-house financing) to get your home construction started.
Types of Prefab Homes
There are several different types of prefab homes. According to the National Modular Housing Council (NMHC), factory built homes that must meet state or local building standards include the following types of buildings.
1. Modular Homes
Modular homes consist of one or more modules that are manufactured in a factory (according to the state and local building codes where the home will be built) and then transported separately to the building site, where construction is completed. Each module usually comes fully-outfitted with interior fittings such as plumbing, electrical, doors, closets, and stairs, so there’s little finishing work to be completed when the home is assembled.
Build times from the point of order to move-in take roughly three to four months. Companies such as Blu Homes and Method Homes offer modular homes.
2. Panelized Homes
Panelized homes are built in panels — a whole wall, for instance — then each panel is transported to the building site and is constructed into a home. Typically, panelized homes require more finishing work than modular homes, as the interior finishing work, such as painting, installing cabinetry and stairs, and installing flooring, must be completed on-site.
Factory build-time is still similar to that of modular homes (about 6 to 12 weeks), but on-site build time is longer. It might take a week to construct the panels onsite, then it could take an additional month to complete the interior work, depending on the schedules of the subcontractors. Total build time typically takes three to five months, depending on subcontractor schedules.
Davis Frame Co. and Amwood Custom Homes are two examples of panelized home manufacturers that can deliver a wide variety of home styles, such as Cape Cod, modern, ranch, or French country.
3. Precut Homes
Precut homes are “kit” homes, such as log cabin kits or dome homes. The homes are cut to design specs in-factory, then are shipped as a kit to the building site to be constructed on-site. Some precut homes are panelized homes, but not all panelized homes are precut homes.
One factor that sets apart precut homes from panelized homes is that precut homes are often designed for the motivated home buyer who wants to construct the home on-site themselves using the materials and instructions supplied by the manufacturer. The kits come with a detailed list of instructions and parts, much like a piece of Ikea furniture. The home buyer then works to piece the home together, either on their own or with the help of a general contractor.
The basic difference between a panelized home and a kit home is intention — most panelized home builders design the panels to be pieced together by their company on-site, while kit home builders just send an instruction manual, unless construction is an add-on feature.
Not all precut homes come with full walls or ceilings pre-manufactured. For instance, some precut log cabin homes simply provide the precut logs and framing materials ready to be assembled on-site. These tend to have the longest on-site build times, which range drastically depending on whether the home buyer completes construction him- or herself, or if he or she enlists the help of a contractor. Total build time typically lasts a minimum of five months, although it could take much longer.
Appalachian Log Structures is one example of a manufacturer of log cabin precut homes, while Timberline Geodesics is an example of a precut dome home manufacturer.
4. Shipping Container Homes
Shipping container homes (homes made, quite literally, from industrial steel shipping containers) made a splash in the media in the 2010s because of their funky and increasingly creative designs. Much like modular homes, shipping container homes can be stacked and pieced together like Legos to create homes, offices, and funky eateries, such as Container Bar.
However, before you settle on shipping container building, just be aware that it’s not the same as building a prefab home. Shipping containers may be sturdy and strong, but they aren’t designed for residential use.
This means you need to check your local building codes to see whether they impose more restrictions for building homes using shipping containers. And unless you’re handy with a welding torch, you’ll likely need to hire an architect and general contractor to figure out exactly how to construct the home.
If you love the look and feel of shipping container homes, there are a few modular manufacturers who offer shipping container building designs specifically for residential and commercial use. For instance, Honomobo sells high-end modular homes built with shipping containers. As you can imagine, the homes can withstand worldwide shipping.
Size and Aesthetics of Prefab Homes
The sky’s the limit when it comes to prefab home size. There are tiny modular structures, such as New Frontier Design’s models. Then there are sprawling, several thousand-square-foot options, such as Blu Homes’ Breezehouse, which offers up to five bedrooms and five bathrooms, and almost 3,000 square feet of space.
One reason modular homes have become so popular is because they meld nicely with the small house trend. Building a house of any size is never cheap, but those who want to keep costs and energy expenses low can opt for a tiny, pre-built modular home that requires much less in terms of foundation and utilities expenses, and can be constructed much faster than a stick-built home.
If you’re interested in building a prefab home, you really aren’t limited by aesthetic. You may just have to choose a particular type of prefab home based on your style preferences.
- Modular Homes: Most modular homes have a sleek, modern, boxy look because the modules are built in squares or rectangles that are then stacked or arranged onsite according to the predetermined building plans. However, some modular builds are combined with panelized walls or roofing that changes the boxy appearance into almost any style of home.
- Panelized Homes: Panelized homes can be built in almost any style or aesthetic according to the home buyer’s preference. Because the homes are built in panels, they can be constructed on-site in a variety of home styles with few limitations.
- Precut Homes: Particularly considering dome homes and log cabin kits, precut homes are often a specific aesthetic. These aesthetics vary depending on the type of kit you choose. There are actually a wide variety of aesthetics to choose from.
Some manufacturers combine different types of prefab building methods to open up the aesthetic possibilities. For example, Westchester Modular Homes builds a home’s rooms and structure using pre-constructed rectangular modules, but then uses panelized walls and roof trusses to change the style and appearance of the home.
Home Package Inclusions
When considering a prefab home, it’s very important to pay close attention to what is and isn’t included in the home package you select. For instance, modular homes are often (but not always) sold with a full package of fixtures, appliances, windows, and flooring, while precut and panelized homes often consist just of the materials necessary for a wall, roof, or frame.
These walls and roofs may or may not include insulation, wiring for electrical, windows, doors, or even drywall. In some cases you can pay additional for the completed wall structure, but in most cases you have to work with an onsite contractor to help you complete and finish your home, including the finishings of the roof and walls.
As an example of what you can expect to be included in each type of structure, consider Stillwater Dwellings. The company offers modular and panelized prefab options, making them a great resource for comparison.
1. Modular Dwelling
With a Stillwater modular build, a buyer might expect to receive:
- Architectural components, the building’s blueprints and design
- Structural engineering, to ensure the structural integrity of your home
- State or local building permit
- Floor structure (not including foundation)
- Roofing
- Lighting fixtures
- Plumbing fixtures
- Windows
- Siding
- Cabinets and trim
- Flooring
- Countertops
- Appliances
- Smart home automation system, to remotely manage electricity use, lighting, and security systems
- Installation of home on prepared foundation
There are upgrade and personalization options available, but these are somewhat limited. Essentially, you choose one of the company’s three finish packages (appliances and fixtures) to achieve the interior aesthetic you’re going for, and you let them do the work.
Some other modular home builders, such as Blu Homes, do offer a greater variety of finishing packages, enabling you more personalization of your home’s finished appearance, but you’re still fairly limited relative to what you can buy on your own. You can’t simply choose a Wolf appliance package if the company doesn’t offer it. You’d either have to opt not to receive the appliances in a package, or you’d have to choose from the appliances the company offers.
2. Panelized Prefab
Stillwater’s panelized prefab homes, as well as other panelized home builders, have fewer inclusions, which can be viewed as positive or negative. If you want more control over the final aesthetic of your home, picking and choosing appliances and fixtures yourself, then panelized construction is your best bet. But if you’re more concerned with a quick build, and you just want to choose a design package that’s already been selected, then modular builds are probably best.
With a panelized home from Stillwater Dwellings, you receive:
- All major framing components (walls and roof)
- Architecture – the blueprints and design
- Structural engineering – ensuring the panels and their placement on your foundation are structurally sound
- State building permit
What’s Typically Not Included
Don’t get lulled into a happy sleep with the phrase “all inclusive” when it comes to buying a modular home — it can be misleading. Understand that the base price of a prefab home doesn’t account for many of the expenses required to build a home.
You must be prepared to pay additional expenses, which may include:
- The land the house will be built on
- Soil testing
- Site survey
- Utility hookups, if necessary — water, waste water or septic, electrical, cable
- The prepared foundation for the home to be built on — concrete slab or pier and beam framing
- Landscaping
- Driveways and sidewalks
- Garage or carport, though these may be available from some manufacturers
- A local contractor or builder to finish the interior of a panelized or precut home
These expenses vary widely based on location, size of home, and even municipal requirements or personal preference. For instance, if you’re building in the country, you may not need or want much in the way of outdoor landscaping. However, if you’re building in the city — or in a neighborhood with strict homeowners’ association standards — you may be required to put in some kind of landscaping.
All told, you can expect to spend possibly tens of thousands on permits, fees, foundation, and utility hookups. You’ll pay more if your property isn’t served by a local sewer and water system and you’ll need to put in a septic system and well.
Before committing to a particular home or manufacturer, make sure you speak extensively to the company about what it provides, and what you’re expected to manage separately. Also, when comparing manufacturers, get specific information about what each company provides so you’re positive you’re comparing apples to apples.
For instance, some builders may offer a more turnkey service, including site prep, soils testing, and foundation preparation. You’d hate to rule out a turnkey service just for being more expensive on the surface, when in reality the total cost differences might be negligible.
Options and Upgrades
In addition to the modular home finishes that come standard in a preselected home build, it’s important to understand that there may be a selection of upgrades to choose from for an additional price. For instance, pieceHomes offers a single finish package, but you can upgrade items, such as opting for bamboo floors instead of cork floors.
Other modular home manufacturers offer more options when it comes to customizing your final project. To get an idea of the types of options or upgrades you may be able to make, check out Blu Homes’ configurator. It enables you to first select a home based on pricing, size, and style; then, once you’ve selected the floor plan you like, you can make alterations to the color finishes, the doors, baseboards, appliance packages, and more.
While Blu Homes has many more options than pieceHomes, you still don’t have as many options as you would have if you were working with a designer or simply shopping online for the perfect finishing touches.
Remember that many of the options and upgrades come at an additional price. If you’re working within a tight budget, be careful when selecting upgrades.
Price
One of the major selling points of buying a prefab home is that, generally speaking, they’re less expensive to build than a stick-built home. Modular Homeowners estimates that the average cost per square foot of a completed home to be built — not including the cost of land (including taxes or fees), the setup of utilities, or exterior touches (driveways, landscaping, and porches) – is $110.
However, many modular home builders command a price much higher than that due to their designer finishes — closer to the $220 per square foot range. So to build a 250-square-foot home, you could expect to pay between $27,500 and $55,000, and if you want to build a 2,500-square-foot home, you could expect to pay between $275,000 and $550,000, not including the cost of land, site costs, or taxes.
There are a couple reasons why prefab homes tend to cost less than site-built homes:
- Less Waste. When you have several groups of contractors delivering materials to a site and building a house on location, there’s a lot of waste created in the form of excess materials. When a home is built in panels or modules in a factory, the system can be improved and waste can be reduced.
- Less Labor and Time. During a traditional build, multiple groups of subcontractors — such as plumbers, electricians, painters, and framers — all come out separately to do their designated work. This work is often delayed or hampered by the work of other subcontractors. When modules or panels are built in-factory, the labor can be more effectively managed so that the work is done quickly and efficiently.
Also, buying a modular prefab home is essentially a one-stop shop. While not all finishes are low-cost, you may still get a deal because the modular home builder buys materials in bulk and passes some savings on to the buyer. You also save the stress and time it takes to painstakingly pick out your own appliances and fixtures.
Overall, Modular Homeowners states that you can expect to save approximately 10% to 20% on the total cost of building a modular home as compared to building a stick-built home. These cost savings are expected to be less for a panelized home, as the construction takes longer and you still have to hire a contractor to complete the home once it’s built on-site.
Quality
Modular and panelized homes are often considered safer and better-built than traditional construction. In fact, the Federal Emergency Management Agency (FEMA) has praised them for their ability to stand up to extreme weather.
After a category 5 hurricane hit Florida’s Dade County in 1992, FEMA noted that there was minimal structural damage to modular housing: “The module-to-module combination of the units appears to have provided an inherently rigid system that performed much better than conventional residential framing.”
But it’s not just the module-to-module framing that makes prefab homes more durable. Other reasons include:
- Ongoing Inspections. Prefab homes are inspected and reinspected at every step of the manufacturing process, ensuring that all materials are constructed and built to code. Most site-built homes have fewer inspections, which means some interior framing problems or shoddy workmanship could sneak under the radar.
- Built to Withstand Shipping. Because prefab homes have to be shipped to the building site, they must be able to withstand the shipping process. This means that additional structural support may be added that isn’t added during traditional onsite construction.
- Built in a Safe Environment. Modular and panelized homes are built in a factory that’s safe from environmental stressors. Materials won’t be affected by extreme weather conditions which can damage a home’s integrity even before it’s built.
Energy Efficiency
Prefab homes may be more sustainable than stick-built homes. There are several reasons for this:
- Construction Is Less Wasteful. Because everything’s factory-built, there’s less waste in the form of construction materials.
- Companies Are More Likely to Reuse Waste. The waste that is generated at the factories is often recycled and reused. For instance, many prefab log home manufacturers grind the unused logs and wood into wood chips or pulp to be sold or reused onsite.
- Seams May Be Tighter. Factory-built homes made with factory-made parts may have tighter seams than traditional stick-built homes, which means less air escapes between rooms or the outside environment. Tight seams help to contain the heat or air conditioning you use. Also, when room-to-room seams are tighter, you can easily separate your home into zones by opening or closing air vents, ultimately using less energy to heat and cool the areas you use the most.
- Energy-Efficient Options Are Offered. Many modular homes that offer finishing packages include energy-efficient and sustainable materials, such as Energy Star appliances and cork or bamboo flooring. You may even be able to find modular home builders that offer upgrades to solar panels or energy-efficient tankless water heaters.
Building a Prefab Home
It’s one thing to understand the ins-and-outs of what a prefab home is, but it’s quite another to undertake the actual building and construction of your home. The good news is that the process isn’t all that different from that of a traditional-build home, but it goes faster.
Before You Start: Buying the Right Land
Even though prefab construction is widely accepted as a quality form of home-building, buying the wrong piece of land can add thousands of dollars to your total cost, or even waylay your plans entirely. Consider the following before buying a home tract:
1. City or Neighborhood Building Restrictions
Always check the city’s and neighborhood’s building ordinances to make sure you’re allowed to build a prefab home — or more specifically, the type of prefab home you want to build. For instance, some neighborhoods require landowners to use specific builders or to build homes to a specific aesthetic. If your dream home is a geodesic dome, it may not fit into a neighborhood filled with ranch-style homes.
2. Easy Access
Remember that your modules, panels, or kit must be delivered to your home via oversized truck. If you’re constructing a modular home, a crane is used to place the home on top of the foundation. If the only way to access your home’s plot is by narrow, windy roads, or if your building site is tucked away behind a forest, you may be in for a rude awakening when it comes to site preparation costs.
My husband and I had to pay an additional $3,000 to have the cedar trees cleared from our property in order for the construction vehicles to access our building site. That’s $3,000 I would have liked to spend elsewhere. If you can find a nice plot of land that’s easily accessible by road, you’ll be able to save money in the long run.
3. Soil Sample
Before you buy your land, check with the current landowner to see if you can pay for exploratory digging or a soil survey. The type of soil your home is built on can significantly affect the cost of laying a proper foundation. For instance, a home built on clay soil or atop significant rock can skyrocket your foundation expenses. The fine sediment of clay expands when it gets wet, then contracts when it dries out.
This constant expansion-contraction can lead to irregularity in the “settling” of a home, opening it up to cracking and shifting of drywall, windows, and doors, and problems with utility connections. A home built on clay should have its soil pre-compacted before the foundation is laid, and in some cases, it may need support beams fitted under the home to prevent damage from shifting soil.
On the other end of the spectrum, if your land consists of too much rock, it can be quite expensive to drill through to create a level foundation. That’s one of the reasons why our septic system cost $13,000 to install — it took three solid days for a drilling company to drill through the rock where our septic system was laid.
There’s not a right or wrong type of soil to build on, but you do want to know what you’re working with before you buy your land so you can account for the costs of proper site preparation.
4. Utilities
Assuming you want to use utilities like water, gas, and electricity, it’s important to check with your city or county to see where the closest hookups are to your desired building site. You’ll likely have to pay for hookups to these services. Otherwise, if you live outside a municipal district, you may have to pay to install a well or septic system. It’s important to know what you’ll have to do (and how much you’ll need to pay) in order to make your home fully functional.
Financing and Choosing Your Home
The process of receiving financing and selecting your home go hand-in-hand. It’s tricky, because you need to know how much home you can afford before choosing a manufacturer or piece of land, but you can’t finalize your loan until you’ve contracted with a home manufacturer.
Luckily, the actual financing of a prefab home is very similar to that of stick-built homes. You can still take out a conventional mortgage in most cases. Just remember, when you talk to banks about taking out a mortgage, you need to factor in all the costs — the costs of the land, the home, and the additional expenses you’ll undertake to prep the land and finish your build.
Also, it’s important to remember that home construction requires a greater down payment than many pre-built homes. You’re likely to be expected to put down a minimum of 20% on the total cost of your home build.
Follow these steps to obtain financing.
1. Get Prequalified
A bank can prequalify you for a construction-to-permanent mortgage loan based on your income level and credit score. It’s a good idea to seek out a minimum of three loan estimates to help you choose the best loan. This can be accomplished in just a few minutes with Credible*. Rates for these loans are typically slightly higher than standard 30-year mortgages.
2. Find Your Land
If you haven’t already selected a site to build on, now’s the time. You may find that in some cases you have to purchase the land first before taking out a construction loan. If this is the case, talk to your bank about the best way to handle the situation. You may end up taking out two loans: one for the land, and one for the home construction.
While land loans are possible to secure, they’re usually at a higher interest rate, and require a minimum of a 20% down payment. If you haven’t purchased your land prior to your build, but you have an “intent to sell” document from the landowner of the price of the land, you may be able to wrap the land purchase into your total construction loan.
3. Choose a Manufacturer
After you’ve selected your land, it’s time to choose a manufacturer. Look for manufacturers with a good reputation and a solid portfolio, as well as design plans that appeal to your aesthetic. Talk extensively to preferred manufacturers before making a selection to make sure you know exactly what they provide. You need to account for any additional costs separately.
4. Select a General Contractor
Some prefab home manufacturers can help you find a qualified general contractor in your area, but if they don’t, you need to find one on your own. Look for someone with extensive experience in prefab home building, who completely understands the steps necessary to prep a building site and arrange for the “buttoning up” of the build post-delivery.
Your general contractor is your go-to person whose job it is to make sure your home’s construction, placement, and finishing is done correctly and to code. Because you’ll work intimately with this individual, interview several candidates before making your selection. After selecting a general contractor, make sure you have his or her price estimate in hand so you include it with your loan agreement.
5. Finalize Your Loan
Go to your preferred bank with your home contract from the prefab builder, general contractor contract, and your land contract (or a letter of intent to sell from the buyer) in-hand. If your home manufacturer doesn’t want to finalize a contract until you have a loan, you may be able to use a drafted contract in its place, showing the bank the intent to finalize.
You also need to provide the bank with your income information, tax returns, proof of employment, work history, credit history, and blueprints of the home for appraisal. The bank should be able to provide you with a detailed list of everything it requires.
6. Set Up a Payment Schedule
You need to work with the bank, the contractor, and the manufacturer to set up a schedule of payments. Usually the bank won’t release the requested money until it has inspected the property to ensure the predetermined work was completed.
7. Close the Loan and Build the Home
Once the loan closes, you can start on construction.
Because you’re undergoing new construction, it’s important to understand that most banks will approve a construction loan that transfers to a permanent mortgage after the home construction is complete and a final inspection has been performed. While the home is being built, you only pay the interest on the construction loan. Once the loan is transferred to a permanent mortgage, you start paying principal and interest based on the terms of your loan.
Remember, because your loan is likely to start out as a construction loan, you’ll most likely be required to pay a 20% down payment on your total construction loan, which may or may not include the cost of your land. This is because construction is a more risky undertaking for banks, so they’re unlikely to offer the lower down payment options often seen with traditional home loans.
Timeline
Just because a prefab home can be built in a matter of days or weeks does not mean that the process is that short. Modular Homeowners suggests that if you’re organized and ready to go, you can build a modular home in a matter of about four months, from planning to move-in. That said, most modular and panelized home manufacturers suggest allowing at least two to three months for home fabrication, so it’s reasonable to estimate it could take from four to six months to go through the entire process from start to finish.
According to 2022 Survey of Construction from the Census Bureau, the average single family home takes seven months to build, from permit to completion, with homes built on an owner’s property averaging roughly eight months. This means that choosing a prefab home could save you between two and four months, depending on the specifics of your build.
There are three general phases to prefab home construction.
1. Planning
The planning phase is actually the least predictable phase in terms of length. This is because depending on where you live, where you plan to build, and what the real estate market is like, it may take time to find the perfect home site, secure building permits, finalize home details, interview and select a general contractor, and close your home loan.
Expect a minimum of one month to complete this phase. Also, remember that many prefab builders can take care of some of this work for you, particularly the process of securing building permits. As long as you’ve already selected your prefab home builder, some of these tasks can be undertaken simultaneously.
2. Manufacture and Site Prep
The manufacture and site prep is pretty predictable in terms of time, but may vary based on the manufacturer you choose and its specific manufacturing timeline. For instance, Modular Homeowners suggests you allow six weeks for the build and prep, but many modular manufacturers, such as Hive Modular, suggest a longer time-frame – often two to three months.
Keep in mind that this middle phase is also affected by your general contractor’s schedule. If he or she can’t complete prep work on the site due to bad weather or scheduling problems with subcontractors, your schedule may be pushed back even if your prefab home is ready to go.
3. Construction
This is when the magic happens — your home arrives and is put in place. But just because you think you’re at the finish line doesn’t mean you’re quite there yet. A modular home can be delivered and put together in a matter of days, but it still takes time to “button up” the site post-delivery.
For instance, it needs to be weatherproofed to prevent water from seeping between the modules. The utilities need to be connected, both inside the home and outside to the grid. The interior walls need to be fastened. And inspections need to be completed.
If you’re constructing a panelized or precut home, even more needs to be done for your home to be move-in ready. All the interior fixtures need to be installed and the finishing completed. You should expect a minimum of six weeks for this phase before you can move into your home.
Pros & Cons of Prefab Homes
Building a home of any kind has pros and cons, but prefab home building is an excellent way to control costs while moving the process quickly along. Pros and cons vary based on your particular situation, budget, preferences, and timeline.
Advantages
- Less Expensive Than Traditional Home Builds. Costs of prefabs are typically cheaper than stick-built homes by an average of 10% to 20%.
- Faster Than Traditional Construction. Generally, it takes one to four months longer to build a traditional home than to construct a prefab.
- Flexible Size and Aesthetic. There are many options when it comes to design, layout, and size.
- Modulars Offer “One-Stop Shopping” Options. Modular home packages are often “all inclusive.”
- Financing Is Available. Financing a prefab home is similar to financing traditional home construction.
- Energy Efficient. The way prefab homes are built, the materials they use, and the airtight construction combine to create a highly energy-efficient space that can reduce ongoing utility bills.
Disadvantages
- Lots of Juggling, Especially During Planning. Finding land, selecting a manufacturer and a general contractor, working with a bank to get a loan, and making sure you know exactly what is being provided and what you’re responsible for may be more overwhelming than working with a custom home builder or architect.
- Some Limitations. If you’re working with a modular manufacturer, the fixtures and interior fittings you can select may be limited.
- May Be More Expensive Than Buying an Existing Home. It may be possible to find an existing home suited to your tastes that’s less expensive than a prefab home.
- More Time-Consuming Than Buying an Existing Home. You may be able to find and move into an existing home in a matter of a couple months or even less.
Final Word
All-in-all, prefab home building is a quick and cost-effective way to build a home when compared to building a traditional stick-built home.
Do your research, talk extensively with each manufacturer you’re considering, and take ownership in your home’s construction. If you want to sit back and let someone else do all the planning and prep work for you, building any home, much less a prefab home, may not be the right choice.